Britishvolt collapse should spark debate on whether it was actually needed
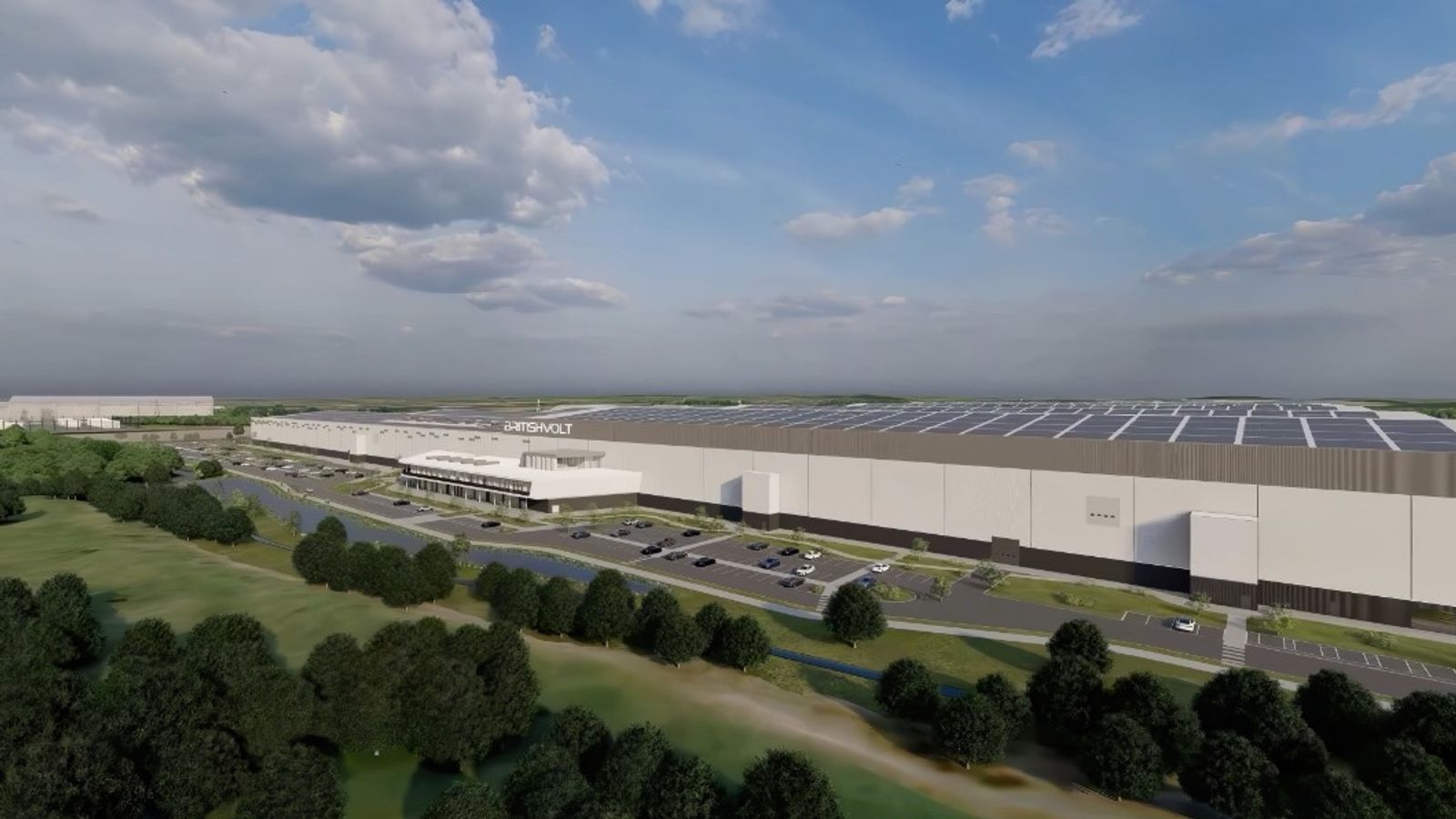
The collapse into administration of Britishvolt will rekindle concerns for the long-term future of the British car-making industry.
The sector is under extreme pressure to pivot from making cars powered by the internal combustion engine to electric vehicles (EVs). To that end the UK government has decreed that, from 2030, no new petrol or diesel cars will be sold in the UK.
Central to that transition to EVs is the need for a number of new ‘gigafactories’ – plants that could produce electric car batteries at scale – and the Johnson government had targeted at least seven or eight of them.
The assumption among industry analysts is that, due to the weight of EV batteries and the expense of transporting them, they need to be located near to the carmakers. Hence the need to build them in the UK.
That need for local sourcing is amplified by ‘rules of origin’ provisions in the UK’s Brexit deal with the EU which require that 70% of a battery must be built in either the UK or the EU for the EV it powers to be sold tariff-free in the bloc. Four in every five British-built cars are exported and just over half of them are sold to countries in the EU.
It is why Britishvolt was promised £100m from the Automotive Transformation Fund, the £850m taxpayer-backed programme aimed at supporting the electrification of Britain’s automotive supply chain.
So the failure of Britishvolt will be seen as a severe setback to the country’s ambitions for EVs. It casts doubt over what is one of only two gigafactories in the UK towards which meaningful progress was being made, the other being built at Sunderland by the Chinese battery maker Envision, which is partnering Nissan locally.
Yet some will argue it is premature to extrapolate Britishvolt’s woes to wider prospects for gigafactories in the UK.
Britishvolt has been seemingly cursed from the off.
Advertisement
Its co-founder, Lars Carlstrom, left the company nearly three years ago after it emerged he had been convicted for tax offenses in his native Sweden. There was then confusion when the company announced its factory would not be in Bridgend in south Wales, as originally intended, but at Cambois near Blyth, in Northumberland, where it had been offered more attractive financial incentives to locate.
In the meantime, the company continued to rack up costs, with the monthly salary bill for its 300 employees reported to be £3m.
Britishvolt then pushed back the planned start date for production to 2025, blaming Russia’s invasion of Ukraine for pushing up costs, while a request for government support was made. It later emerged that management had put the company on what was described as ‘life support’ in July.
Then, in August last year, Mr Carlstrom’s co-founder, Orral Nadjari, unexpectedly resigned.
The Guardian newspaper subsequently reported details of his extravagant spending, revealing that the company had leased a seven bedroom £2.8m mansion with a swimming pool and jacuzzi for executives, as well as hiring a Dubai-based fitness instructor to conduct yoga classes for staff remotely.
Lack of firm supply deals with carmakers
Graham Hoare, the respected former head of Ford of Britain, was hired in his place as an interim chief executive and, in November, the company secured an emergency lifeline from Glencore, the commodities trading and mining giant, which was one of its shareholders.
But at the heart of its problems was that it had never signed firm supply deals with carmakers sufficient to guarantee future revenues of the kind that potential investors would have wanted to see.
All it had were preliminary agreements with two luxury carmakers, Aston Martin and Lotus, to design batteries for their EVs.
Last week, the company said it was in talks to sell a majority stake in itself to a consortium of investors in order to secure its future, but those came to nothing.
Today brought the news, which had seemed increasingly inevitable, of administration.
That need not be the end of the story.
Britishvolt’s main asset, the site at Cambois, is well-located close to a deep-water port and enjoys both good rail links and access to clean energy from Norway. It is highly likely to attract potential buyers.
India’s Tata Motors, the owner of Jaguar Land Rover, has been suggested as a possible buyer although it is hard to see why it would want to own a site in Blyth when a site in Coventry, much closer to the bulk of its manufacturing facilities elsewhere in the West Midlands, remains possible for development.
The bigger questions and concerns
Perhaps the bigger question – and concern – is how many car manufacturers will be in need of British-made EV batteries come the end of the decade.
Honda has already closed its plant at Swindon in Wiltshire while Stellantis, the Fiat, Peugeot and Citroen combine, is ending volume car production at Ellesmere Port in Cheshire and converting production there to electric vans and cars whose battery cells will be sourced on mainland Europe.
Mini’s owner, BMW, has confirmed the next generation of the model’s electric version will be built not at Cowley in Oxfordshire but in China. And it is not yet clear from where the luxury British carmakers Rolls-Royce and Bentley, respectively owned by BMW and Volkswagen, intend to source their batteries as they switch to EV production. Nor are Toyota’s intentions clear for its site at Burnaston in Derbyshire.
The biggest question of all concerns Jaguar Land Rover which, it seems, is likely to be relying on European production for at least some of the batteries powering its UK-built vehicles.
So perhaps the bigger worry is not the lack of gigafactories but whether they will actually be needed amid declining output from British-based volume car producers.